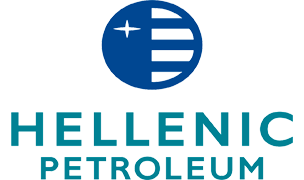
€22 mil. on safety improvements
in all Group facilities in Greece and abroad
60% reduction in Lost Workday Injuries
in comparison to last year
500,000 hours without any lost workday injuries at the Aspropyrgos refinery
1,000,000 hours without any lost workday injuries at the Elefsina refinery
1,000,000 hours without any lost workday injuries at the Thessaloniki refinery
2,000,000 hours without any lost workday injuries at the Headquarters
300,000 hours without any lost workday injuries at the subsidiary company DIAXON
Why is it material?
Employee Health, Safety & Well-being are the Group’s most important priority and of fundamental corporate value for all its activities, because they are interconnected to its business success.
Continuous improvement and the achievement of excellent performance in both Process and Personnel Safety are the cornerstone of our day-to-day operations and motivate us to achieve our goals.
Our four main pillars of action are: 1) Leadership and commitment, 2) Consolidation of a safety culture, 3) Improving performance – safety indicators, 4) Lessons learned from incidents and follow-ups.
Our approach
The Group promotes Health, Safety and Well-being in the workplace by:
- Strengthening risk prevention and mitigation measures.
- Being committed to providing the resources needed to meet Health and Safety goals and to continually improving the Health and Safety Management System.
- Ensuring consultation with all stakeholders and meeting the needs of society.
The above three principles are clearly stated in the Company’s Policy and through strong Leadership (leading by example); they also comprise its commitment.
“Risk Assessment”, which is at the core of the Safety Management System, is supported and reinforced through procedures, audits and safety training.
The Group upholds that “Safety concerns everyone” and not only urges employees to report and investigate incidents near misses and unsafe situations or actions, but also rewards their successful intervention on safety issues.
Our ambition
Our ambition is to be amongst the best in the industry, and to create a working environment throughout all activities with zero accidents and occupational diseases.
Through strong leadership and total personnel involvement, we seek to prevent and protect Health and enhance the Safety of employees and contractors from possible impacts that could arise during the facilities’ operation.
Each facility, and the Group as a whole, sets annual measurable Key Performance Indicators for performance improvement, thereby creating a common Group safety culture.
At the same time, we extend the application of our Holistic Safety Management System to our other activities, apart from Refining, in order to consolidate our safety culture and improve our performance.
In the field of occupational risk management, the preventive principle is applied so that potential health and safety risks can be anticipated and controlled.
Specifically, potential risks are identified and controlled according to the criteria set under Greek legislation (Law 3850/2010), as well as European and international standards, codes, and best practices. Each Group facility has a written occupational risk assessment study, which includes measures to be taken to either eliminate or control/mitigate hazards and maintain them at low and acceptable levels(as low as reasonably practical).
Assuring employees’ health is an integral part of the company’s policy and the Health Surveillance Procedure. Periodic employee medical checkups are carried out depending on job description, age group and gender.
Employees’ health surveillance is supplemented with additional medical tests conducted by occupational physicians.
In 2018, approximately €22 million was invested in safety improvement projects at the Group’s facilities in Greece and abroad. These investments do not include the supply of personal protective equipment, the supply and maintenance of instruments and safety equipment and the supply of firefighting materials and other consumables.
Facility | 2018 INVESTMENT (in € mil.) |
2019-2023* INVESTMENT (in € mil.) |
---|---|---|
Aspropyrgos, Elefsina and Thessaloniki refineries | 11.82 | 39.68 |
ΕΚΟ | 6.42 | 14.86 |
DIAXON | 0.00 | 0.09 |
HP CYPRUS | 2.28 | 4.3 |
OKTA | 0.558 | – |
JUGOPETROL | 0.312 | 6.08 |
EKO SERBIA | 0.045 | 1.062 |
EKO BULGARIA | 0.187 | 0.256 |
ΑSPROFOS | 0.03 | – |
Total | 21.65 | 66.32 |
*(approved program)
HELLENIC PETROLEUM S.A., with the aim of continuously improving performance and achieving excellence in Safety, is committed to applying a Holistic Safety Management program across all Group activities based on standards of other large international groups in the oil & gas industry.
In 2015, the Holistic Safety Management program was launched in the Group’s industrial facilities as well as at its marketing company’s airport facilities. The Holistic Safety Management program is based on managing safety in an organized and structured way, which systematizes the required procedures’ implementation.
The Holistic Safety Management program consists of 21 Systems-Pillars for each industrial facilities that covers every aspect of the facilities’ operation.
In order to achieve excellence in Safety, the framework of each System describes the requirements that must be met, the roles and responsibilities regarding their implementation, and the methodology for evaluating and measuring performance.
Within 2018, the operational framework for the 12 critical best practices related to high risk activities was completed and an annual review of the majority of the Systems was carried out.
Each of the Group’s activities (industrial facilities, fuel storage facilities, headquarters) sets annual measurable Key Performance Indicators regarding the improvement of its performance in Health and Safety. The performance, against the set targets, is reviewed on both a monthly and annual basis and the relevant report is presented to Management.
Furthermore, HELLENIC PETROLEUM participates in the benchmarking survey for accidents/incidents which is conducted every year by the European Organization CONCAWE with which it cooperates.
During 2018, from a total of 8,970,070 man-hours worked, there were 17 lost workday injuries for both own staff and contractors (60% less than in 2017), working either at the HELPE refineries and chemical plants or at EKO and at the Headquarters.
1 First aid injuries are not included
2 Absences due to any incapacities (illness, accident) are included
* For detailed information by region and gender, see indicator 403-2 here
The diagrams below show the fluctuation of the Group’s most significant indicators, in comparison with the relevant CONCAWE indicators over the last five years.
Lost Workday Injury Frequency (LWIF) Index
Reduced by 58% for HELPE and EKO compared to 2017
All Injury Frequency (AIF) Index
Reduced by 57% for HELPE and EKO compared to 2017.
Process Safety Event Rate (PSER) for HELPE and EKO*
*Extensive reference to the PSER index is presented at “Leaks and Oil Spills”
In the context of establishing a common safety culture in all of the Group’s industrial facilities, basic training procedure (fire safety, rescue techniques, first aid, etc.) and leadership seminars are applied (from managers to coordinators and supervisors), in order to reinforce and establish a Safety Culture.
Apart from employees, training is extended to contractors, customers, tank truck drivers, petrol station owners, university students and graduates. Visitors are informed through a leaflet concerning onsite safety instructions.
Especially concerning contractor training, training is based on oral presentations by Safety Engineers along with written examinations at accredited training centers and only successful candidates are given an entry card to work in the facilities.
AIC-EIC-TIC | ΕΚΟ | ΟΚΤΑ | DIAXON | HP CYPRUS | EKO SUBSIDIARIES* | ΑSPROFOS | |
---|---|---|---|---|---|---|---|
No. of employees (M/F) | 1877 (1722/155) |
508 (333/175) |
356 (285/71) |
96 (83/13) |
56 (38/18) |
175 (103/72) |
158 (101/57) |
No. of trained employees (M/F) | 1541 (1449/92) |
147 (131/16) |
316 (278/29) |
26 (26/0) |
44 (35/9) |
221 (140/81) |
123 (81/42) |
Training man hours (M/F) | 28448 (26913/ 1535) |
2598 (2533.5/64.5) |
949 (854.5/94.5) |
94 (94/0) |
243 (201/42) |
852 (634.5/217.5) |
425 (387/38) |
No. of trained contractors & others (M/F) | 2882 (2700/182) |
871 (842/29) |
1035 (1025/10) |
0 (0/0) |
58 (56/2) |
433 (361/72) |
0 (0/0) |
Contractors and others training man-hours (M/F) | 14001 (13408/593) |
5634.5 (5410.5/224) |
517,5 (512.5/5) |
0 (0/0) |
132 (127/5) |
1087 (910/177) |
0 (0/0) |
*BULGARIΑ, SERBIA, JP MNE