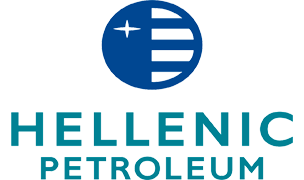
Over €22 mil. investments
in the Group’s industrial facilities
for environmental management projects
& improving the environmental footprint
>30% reduction
of main air emission
indicators over the last 5 years
(tn/throughput)
19% reduction of CO2 emission indicators
(tn/ crude oil throughput) from 2014
(in comparison to initial goal of -5% by 2020)
Why is it material?
Socially and environmentally responsible and efficient operation requires continuous reduction of air emissions in order to minimize our impact and contribute substantially to improving air quality in the locations we operate.
Our socially and environmentally responsible operation builds relationships with local communities based on trust and cooperation. Through the adoption of best available practices and investments in modern low emission technologies, we achieve continuous reduction of air emissions and improvement of air quality.
Our approach
We aim to continuously reduce air emissions by implementing specific actions such as maximizing gas fuel use, using fuels with higher environmental specifications and applying advanced technologies to the production process.
We are committed to strictly complying with all national and European laws and best practices, a case in point being our compliance with petroleum industry’s Best Available Techniques and the European Industrial Emissions Directive.
Our commitment is put in practice through significant investments in modern production & emission abatement technologies. These include low nitrogen oxide emission burners, particle retention filters, volatile organic compound recovery units, sulfur recovery units from exhaust gases, etc.
Our approach and results to date have had particularly positive evaluations, if you take into account the significant reduction of key air emission indices over the last five years as well as our contribution to air quality (as indicated by monitoring results) of the neighboring areas in which we operate.
Our ambition
Our goal is the continuous reduction of air emission indices in all our activities and acknowledgment of our significant contribution to improving the air quality of the local communities.
HELLENIC PETROLEUM aims to reduce air emissions across the range of its activities by implementing specific actions including maximizing fuel gas use, using fuels with higher environmental standards and implementing advanced technologies in the production process (ie. low nitrogen oxide emission burners, steam recovery systems during petroleum products loading).
In the Group’s three refineries, which comprises the company’s main productive activity, fuel gas use for self-consumption has been maximized, i.e. fuels derived from flue gases that undergo treatment to reach zero sulfur content are used in order to limit use of heavier liquid fuels. As a result, significant reductions in sulfur dioxide (SO2) emissions have been achieved.
Along with the important fuel gas desulphurization projects carried out at the facilities, low-NOx burners were also adopted for the majority of combustion sources. The result of all these efforts is the significant reduction of nitrogen oxide emissions in recent years.
To reduce Volatile Organic Compounds (VOC) emissions, Best Available Techniques have been implemented for product storage and transport. These include secondary seals on the roofs of floating roof tanks, white painting of volatile product tanks (for high reflectivity), bottom tank truck loading and Vapor Recovery Systems at loading facilities, and a preventive maintenance program.
Additionally, the particularly effective implementation of leak detection and repair (LDAR) programs with the aim of reducing VOC emissions from equipment (e.g. valves, gaskets, etc.) continues with significant results.
For 2018 specifically, despite the significantly increased operating levels compared to previous years, the indices for sulfur dioxide (SO2), nitrogen oxides (NOx) and particulate matter – PM10 emissions (kg emissions per tn throughput) show significant improvement with a decrease of 31%, 32% and 49% respectively, with PM10 predominating for the last five-years (2018 in comparison to 2013 reference year).
Reductions in air emissions indices over the last five years are presented in detail in the diagram above.
Sulfur Dioxide (SO2), Nitrogen Oxides (NOx) and Particulate Matter (PM10) Indices (kg emissions per tn throughput for 2013-2018)
The small increase in the PM10 index is mainly due to emissions from abnormal operating conditions (temporary malfunction of the catalytic cracking unit of Aspropyrgos refinery, which was solved in a short time). It is noted that a particulate filter investment is planned to further reduce PM10 emissions at Aspropyrgos Refinery within the framework of Best Available Techniques.
Regarding compliance with current legal limits (tn/year), reported SO2 emissions (as an absolute figure, tn/year) remained much lower (-58%) than the current limit of the relevant environmental permits (in tn / year).
Sulfur Dioxide (SO2) emissions for 2013-2018 compared to the current limit
The above performance, in basic sulfur dioxide (SO2), nitrogen oxides (NOx) and particulate matter (PM10) emissions, regarding point source emissions from the industrial facilities’ operation, are also reflected in air quality measurements of the areas in which we operate. These are monitored by our facilities’ Air Pollution Measurement Stations and other respective competent authorities’ monitoring Stations as well (municipalities’ air quality reports and the Ministry of Environment and Energy).
It should be noted that air quality measurements include and correspond to all the surrounding area’s contributing air emission sources, such as transportation and other industrial activities.
Within the context of complying with the Industrial Emissions Directive (IED) and the new limits according to the Best Available Techniques Conclusions for the refining of mineral oil and gas (REF BAT Conclusions Decision), the Group’s refineries have launched additional actions to further improve performance in relation to the monitored quantitative and qualitative indices.
In particular, significant investments have been programmed to further reduce nitrogen and sulfur oxides, particulates and volatile organic compound emissions regardless whether they involve capital expenses (e.g. filters, end of pipe techniques) or operating costs (e.g. increased use of natural gas for self-consumption)
The results stemming from these programs, in addition to the impact from other energy efficiency and savings projects being implemented in parallel, will lead to a further reduction in air emissions.